机车滚动轴承检测的重要性与技术要点
机车滚动轴承作为列车走行部的核心部件,直接关系到机车运行的安全性、稳定性和使用寿命。随着铁路运输向高速化、重载化方向发展,轴承承受的机械负荷、热负荷和环境冲击日益增大,其工作状态直接影响机车牵引性能和轮轨系统的可靠性。因此,滚动轴承的定期检测与状态评估已成为铁路车辆维护体系中的关键环节。通过系统化的检测技术,能够及时发现轴承的早期损伤、疲劳剥落、润滑失效等问题,避免因轴承故障导致的列车脱轨、轮对卡死等重大事故。
机车滚动轴承主要检测项目
1. 外观与尺寸检测:采用高清工业内窥镜和三维测量仪对轴承内外圈、滚道、滚动体进行目视检查,重点检测裂纹、锈蚀、磨损及变形情况,同时测量游隙、圆度、锥度等几何参数,确保尺寸精度符合GB/T 307.1标准要求。
2. 材料性能检测:通过显微硬度计、磁粉探伤仪及金相分析仪等设备,评估轴承材料的硬度梯度、残余奥氏体含量、表面脱碳层深度等指标,判断热处理工艺是否达标,预防因材料缺陷导致的疲劳失效。
3. 振动与声学检测:利用加速度传感器和声发射系统采集轴承运转时的振动频谱,通过特征频率分析(如BPFI/BPFO缺陷频率)识别滚道剥落、滚子划伤等故障,振动加速度值需满足ISO 15242规定的A/B级标准。
4. 温度场监测:采用红外热像仪和嵌入式温度传感器实时监测轴承运行温度,异常温升往往预示润滑失效或装配过紧,正常工况下轴承温升不应超过环境温度45℃。
5. 润滑状态评估:通过铁谱分析和油脂理化检测,测定润滑油的粘度、水分含量、金属磨粒浓度等参数,结合油膜厚度传感器数据,判断润滑系统工作效能,避免干摩擦导致的轴承卡滞。
智能检测技术的发展趋势
当前轨道交通领域正积极推进PHM(故障预测与健康管理)系统建设,通过集成多物理量传感器、边缘计算模块和深度学习算法,实现滚动轴承的在线监测与剩余寿命预测。如基于神经网络的故障诊断模型,可对振动信号进行时频域特征提取,准确率达到98%以上;激光诱导击穿光谱技术(LIBS)则能实现油脂金属元素的快速定量分析,显著提升检测效率。未来,随着数字孪生技术的应用,机车轴承将实现全生命周期健康管理,为铁路运输安全提供更智能化的保障。
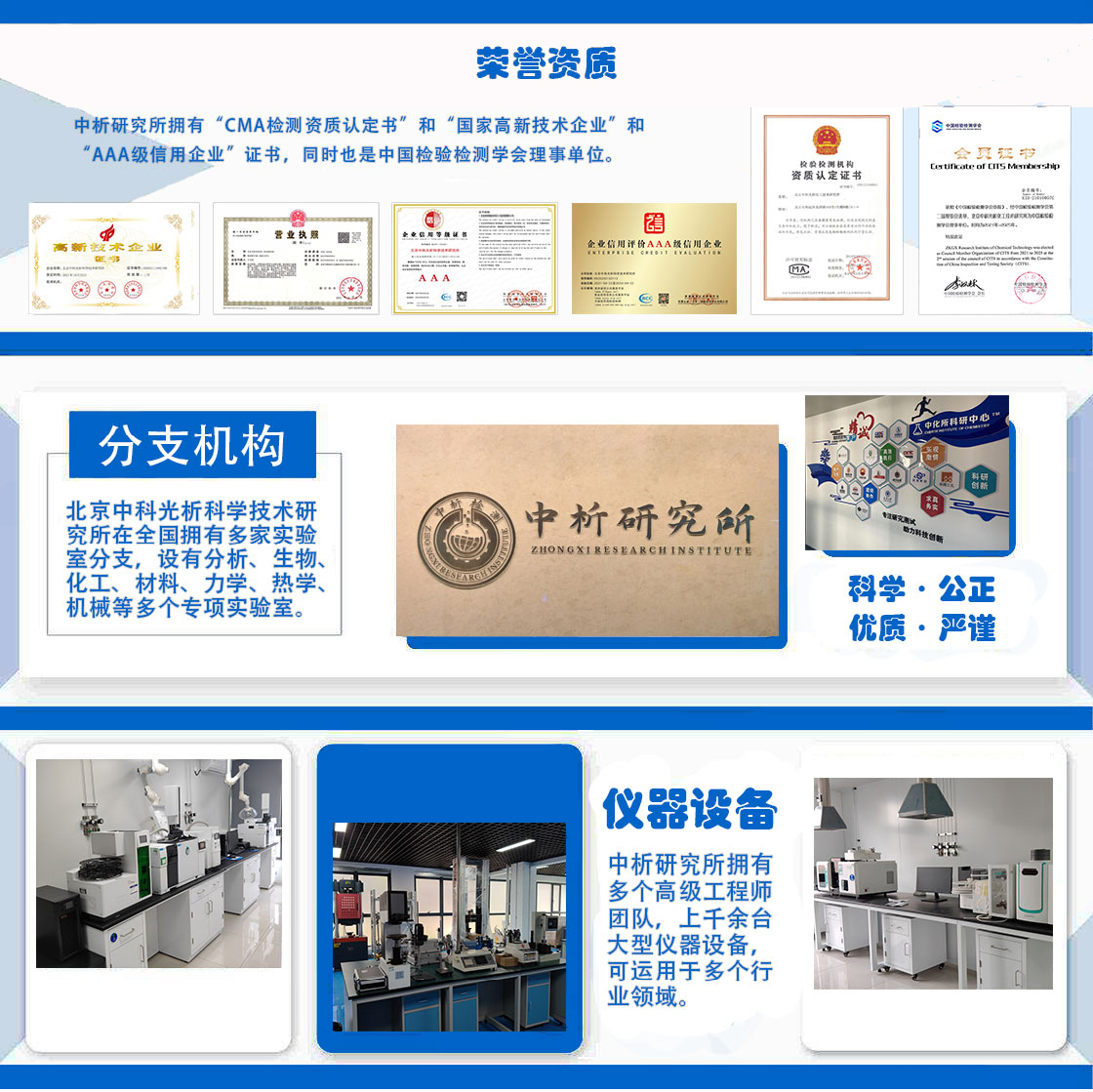
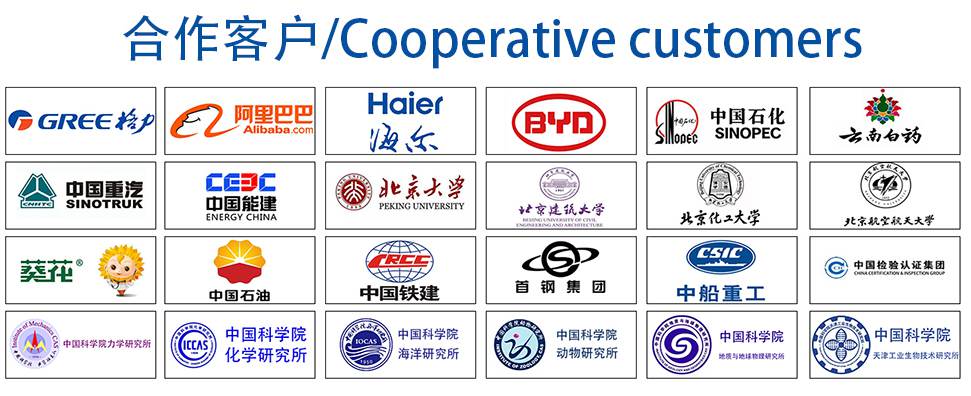