摩托车用锂电池检测:守护安全的关键防线
随着新能源技术的快速发展,锂电池凭借高能量密度、轻量化等优势,正逐步取代传统铅酸电池成为摩托车动力系统的重要组成。然而,锂电池在充放电过程中存在热失控、短路等安全隐患,尤其摩托车行驶环境复杂多变,对电池的可靠性提出更高要求。建立完善的锂电池检测体系,已成为保障车辆安全运行、延长电池寿命、维护消费者权益的行业共识。国际标准化组织(ISO)与各国监管部门已针对动力电池出台超过20项强制性检测标准,覆盖从原料到成品的全生命周期管理。
核心检测项目体系
安全性能测试
过充/过放保护测试:模拟异常充电电压(通常设定为标称电压的1.5倍)持续24小时,验证BMS保护系统的响应速度与切断精度。短路测试通过强制正负极接触,检测电池在极端短路情况下是否能在150ms内启动保护机制,外壳温度需控制在80℃以下。
电化学性能验证
容量衰减测试要求电池在标准充放电循环500次后,容量保持率不低于初始值的80%。低温启动测试需在-20℃环境下持续放电至终止电压,验证电解液低温导电性能。脉冲放电测试模拟急加速工况,检测瞬时大电流(通常为3C倍率)输出时的电压稳定性。
机械结构可靠性
振动测试按照GB/T31467.3标准进行XYZ三轴随机振动,频率范围5-2000Hz,持续时间不少于24小时。跌落测试从1.2米高度进行6面3次自由跌落,要求外壳无破裂、电解液无泄漏。挤压测试采用半径75mm的半球体施加13kN压力,保持10分钟后监测是否发生热失控。
环境适应性评估
湿热循环测试需在温度40℃±2℃、湿度95%RH环境中持续720小时,验证密封件老化情况。海拔模拟测试通过低压舱模拟5000米高原环境,检测气压变化对电池壳体形变的影响。盐雾腐蚀测试依据ISO9227标准进行96小时中性盐雾试验,评估金属部件的耐腐蚀等级。
智能化检测新趋势
当前检测技术正向数字化、智能化方向发展,部分实验室已引入AI视觉检测系统,通过高分辨率热成像仪实时监测测试过程中电池表面的温度场分布,结合大数据分析预测潜在失效模式。某知名检测机构最新研发的电池云端监控平台,能够同步采集2000+电芯的电压、温度数据,检测效率提升300%。
完善的检测体系不仅需要齐全的设备支撑,更依赖专业的技术团队。国内领先的检测机构已建立包含电化学博士、安全工程师在内的跨学科团队,提供从单体电芯到电池包系统的全套解决方案。消费者在选择锂电池产品时,应重点关注是否通过GB38031-2020《电动汽车用动力蓄电池安全要求》等强制性认证,以及是否具备UN38.3运输安全测试报告。
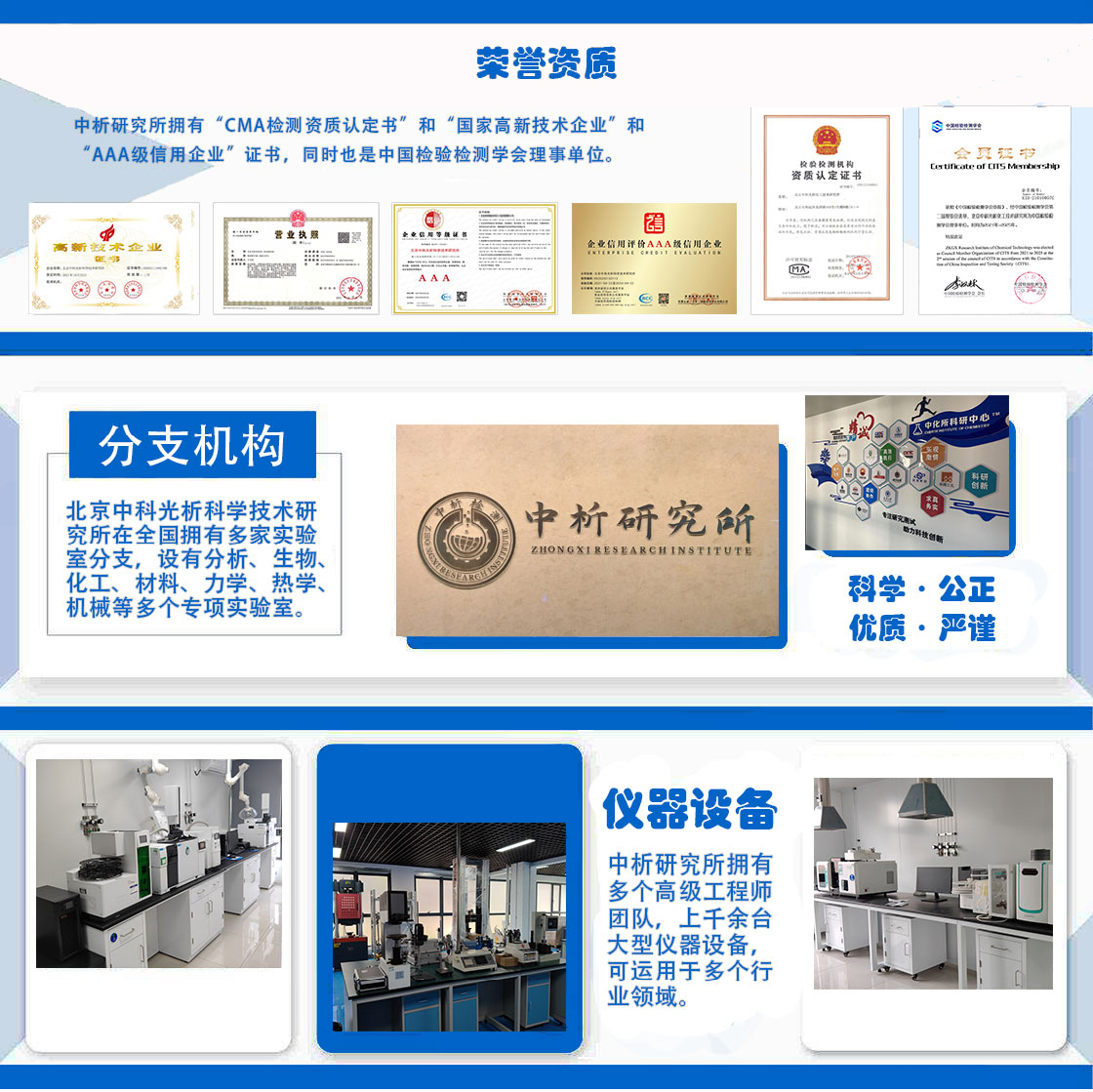
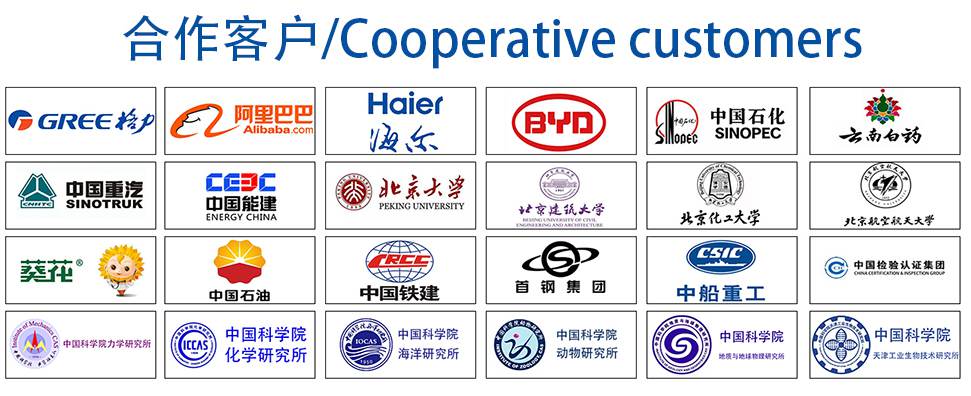