燃料电池电动汽车载氢系统检测
实验室拥有众多大型仪器及各类分析检测设备,研究所长期与各大企业、高校和科研院所保持合作伙伴关系,始终以科学研究为首任,以客户为中心,不断提高自身综合检测能力和水平,致力于成为全国科学材料研发领域服务平台。
立即咨询燃料电池电动汽车载氢系统检测的重要性
随着能源结构向清洁化转型,燃料电池电动汽车(FCEV)因其零排放、高效能特性备受关注。作为核心动力源,车载氢系统的安全性、可靠性和耐久性直接决定了车辆运行性能与用户安全。载氢系统包含储氢罐、高压管路、阀门、压力调节装置等关键部件,其需要在极端温度、振动、压力波动等复杂工况下保持稳定性。因此,建立科学完善的检测体系,对氢气泄漏、材料强度、密封性能等关键指标进行系统化验证,成为保障燃料电池汽车商业化应用的前提。
核心检测项目及技术标准
1. 储氢罐完整性检测
储氢罐作为高压氢气的存储单元,需通过爆破压力测试(≥2.25倍工作压力)、疲劳循环测试(≥15000次充放循环)和渗透率检测(日渗透量≤0.1%)。采用超声波探伤技术检测复合材料层间缺陷,同时通过X射线衍射分析铝合金内胆的应力腐蚀敏感性。
2. 管路系统密封性验证
基于ISO 19880-3标准,对氢气管路进行氦质谱检漏(泄漏率≤0.05mL/min/m)和压力保持测试(1.25倍工作压力下保压30分钟)。采用振动台模拟车辆行驶中的机械冲击,验证管路接头在5-2000Hz频率范围内的抗共振性能。
3. 安全阀与泄压装置检测
通过动态响应测试验证安全阀在超压工况下的开启时间(≤50ms),采用高温(85℃)和低温(-40℃)环境模拟评估泄压装置的启闭灵敏度。同时利用CFD仿真分析氢气扩散路径,确保泄压方向符合安全距离要求。
4. 氢泄漏监测系统校准
在密闭舱体内通入浓度梯度氢气(0-4%vol),校验传感器的检测精度(误差≤±2%FS)和响应时间(T90≤3s)。通过EMC测试验证监测系统在30V/m电磁场干扰下的稳定性,确保误报率低于0.01次/千小时。
检测技术发展趋势
随着IV型储氢罐的普及,基于光纤光栅的实时应变监测、AI驱动的泄漏源快速定位技术正成为研究热点。同时,行业开始引入数字孪生技术,通过虚拟仿真预判系统失效模式,大幅缩短检测周期。预计到2025年,车载氢系统检测将形成"实验室认证+车载实时诊断"的双重保障体系。
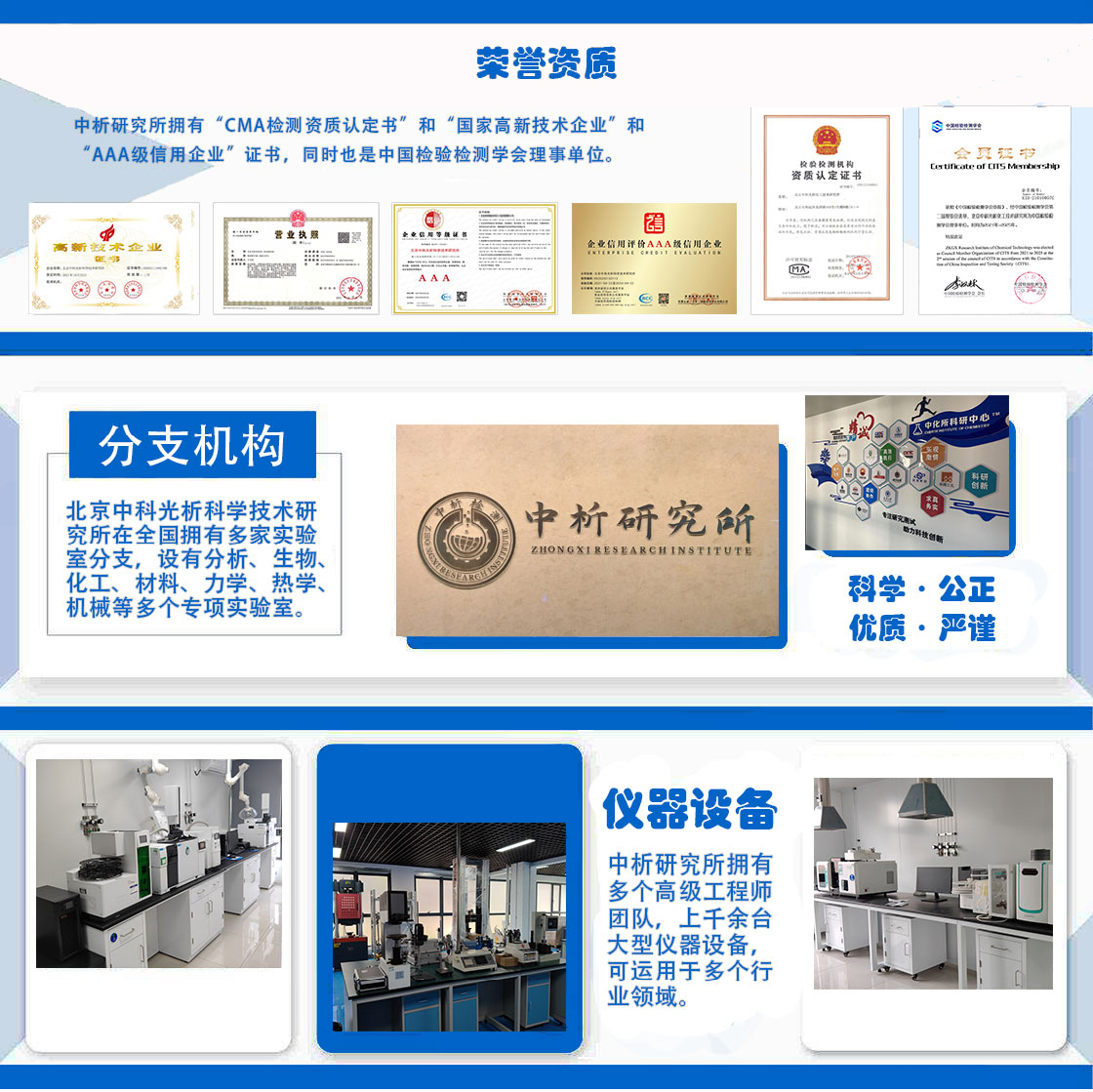
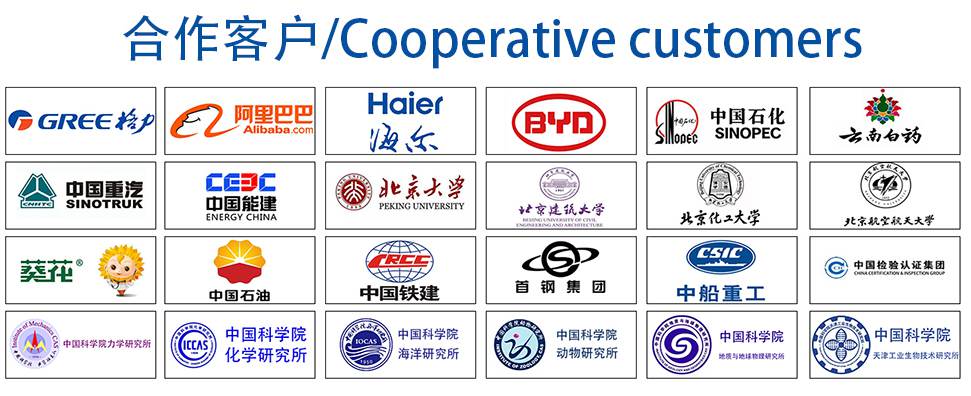