通用设备检测的行业价值与应用场景
在工业生产、建筑施工和日常运维领域,通用设备检测是保障安全生产、延长设备寿命的核心环节。通过系统化的检测流程,能够有效发现设备潜在隐患,避免因机械故障导致的生产停滞或安全事故。随着智能制造技术的普及,2023年行业数据显示,定期实施设备检测的企业设备故障率降低57%,维护成本减少34%,充分印证了检测工作的重要价值。
核心检测项目体系
完整的通用设备检测体系包含六大核心模块:
1. 基础功能检测:包括电源系统核查、控制面板响应测试、传动机构运转监测等基础性能验证,确保设备满足基本运行条件。特殊行业设备还需进行精度校准,如数控机床的定位精度需控制在±0.01mm以内。
2. 结构完整性检测:运用超声波探伤仪、磁粉检测等无损检测技术对关键承力部件进行检查。压力容器类设备需重点检测焊缝质量,依据TSG 21-2016标准进行强度试验。
3. 安全防护检测:涵盖急停装置有效性验证、防护罩完整性检查、接地电阻测量(要求≤4Ω)等安全要素。防爆设备还需通过EX认证检测,确保符合ATEX指令要求。
4. 能耗效率检测:采用电能质量分析仪监测设备功率因数(需≥0.9),使用热成像仪检测电机温升(允许值≤65℃)。空压机等动力设备需进行能效等级评定。
5. 环境适应性检测:包含IP防护等级验证(如IP65防尘防水)、振动测试(频率范围5-2000Hz)及高低温循环试验(-40℃至+85℃),确保设备能在规定工况下稳定运行。
6. 智能化功能检测:对具备物联网模块的设备,需测试数据传输完整性(丢包率<0.1%)、远程控制响应时间(≤500ms)及系统兼容性等数字化指标。
检测技术创新与标准发展
当前检测技术正朝着智能化方向发展,工业内窥镜与AI图像识别结合可实现微米级缺陷自动判别,振动分析系统能提前15天预警轴承故障。GB/T 34370-2017等新国标对检测流程作出明确规定,要求建立包含10大类128项参数的设备健康档案。第三方检测机构提供的CMA认证报告已成为设备验收的必要文件。
通过建立周期性的检测机制(建议重要设备每月1次常规检测),企业可构建预防性维护体系。值得关注的是,设备检测数据与MES系统的深度融合,正在推动预测性维护模式的普及,使设备综合效率(OEE)提升最高可达23%。
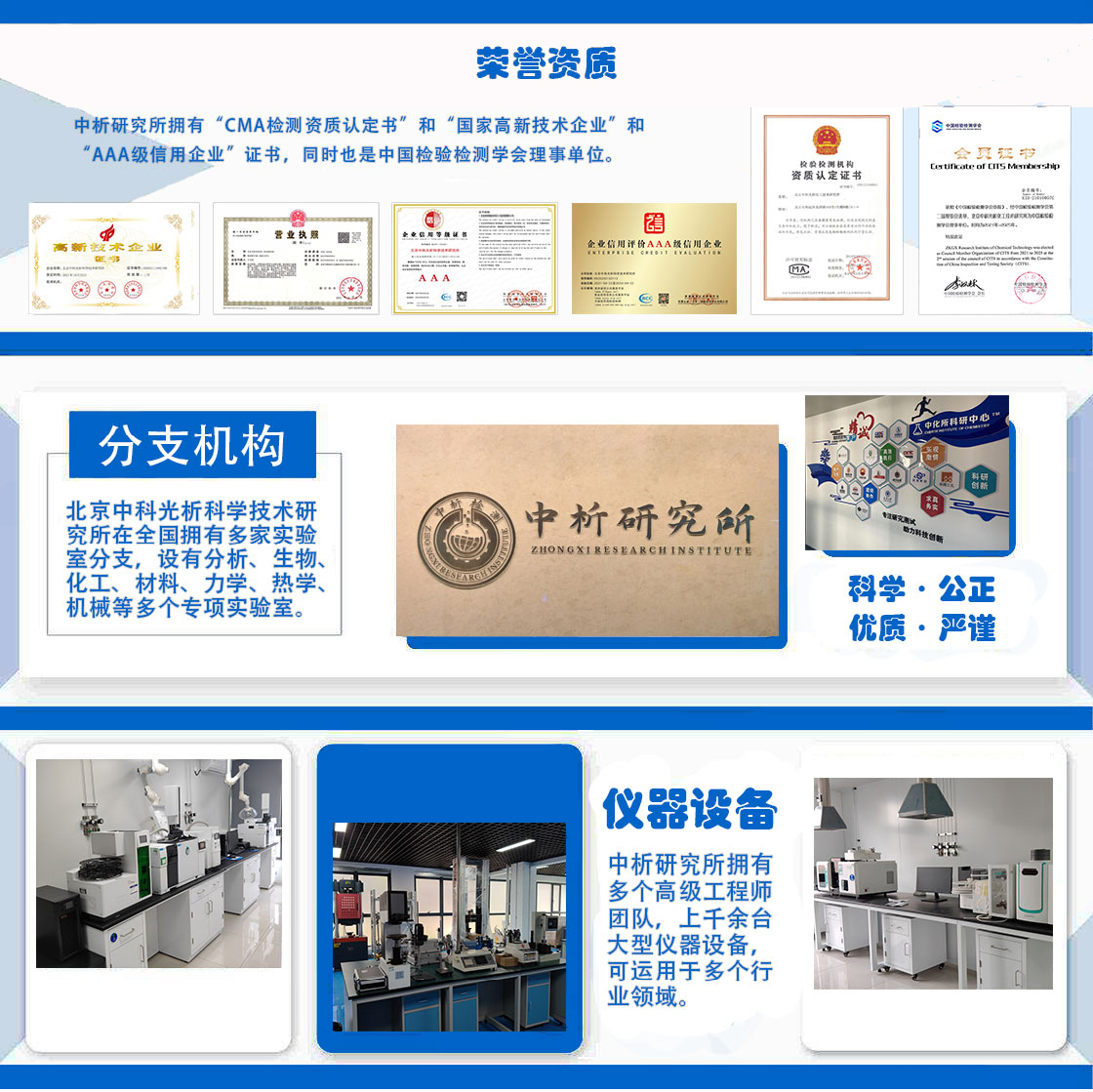
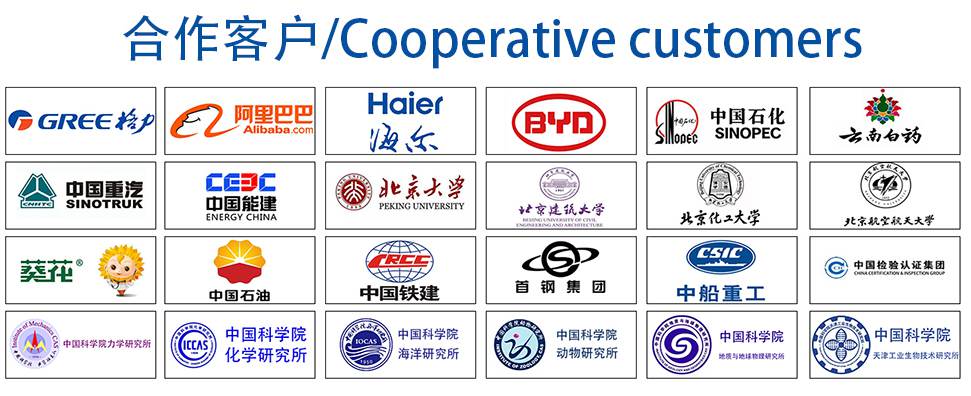