录井钢丝检测项目与技术要求解析
录井钢丝作为石油钻井作业中连接测井仪器与地面的关键承载部件,其性能直接影响井下数据采集的安全性和准确性。由于长期承受复杂工况下的拉伸、弯曲和腐蚀作用,定期开展系统性检测是预防工程事故的重要措施。根据SY/T 6584-2018《石油测井用钢丝绳技术条件》等行业标准,规范的检测项目应包含以下核心内容:
一、基础物理性能检测
1. 外观质量检测:通过目视或20倍放大镜观察钢丝表面是否存在断丝、锈蚀、压痕等缺陷,重点检查接头部位与作业段损伤情况。
2. 直径测量:使用千分尺在非接头段随机选取三个测量点,实测值与标称直径偏差不应超过±0.1mm。
3. 直线度检测:将钢丝自由悬挂后,用钢直尺测量每米范围内的弯曲度,最大偏移量需小于3mm/m。
二、力学性能测试
1. 破断拉力试验:在电子万能试验机上以10mm/min速度加载至断裂,实测值应达到标称破断拉力的95%以上。
2. 残余扭矩测试:将1m钢丝试样自由端固定,测量另一端的旋转圈数,合格标准为≤0.5圈/米。
3. 疲劳寿命试验:模拟作业条件进行3×10^5次循环加载,钢丝表面不得出现明显断丝或结构损伤。
三、材料特性分析
1. 金相组织检测:通过金相显微镜分析钢丝微观结构,确认是否存在过烧、脱碳等热处理缺陷。
2. 化学成分分析:采用光谱仪检测C、Mn、Si等元素含量,应符合GB/T 699对优质碳素结构钢的要求。
3. 镀层质量检验:使用磁感应测厚仪检测锌层厚度,同时进行硫酸铜浸渍试验验证镀层致密性。
四、无损检测专项
1. 磁粉探伤:对整根钢丝实施连续磁化检测,发现表面裂纹深度超过0.1mm时应作报废处理。
2. 超声波检测:采用5MHz探头扫描内部缺陷,重点关注芯丝断裂、夹渣等隐蔽性损伤。
3. 涡流检测:适用于大批量检测场景,可快速识别钢丝直径突变、局部腐蚀等异常信号。
检测周期建议:新钢丝入库需进行全项目检测,在用钢丝每季度开展力学性能抽检,累计使用达设计寿命60%时应缩短至每月检测。当单次作业深度超过5000米或遭遇卡钻异常工况后,必须执行无损检测专项。
通过建立完整的录井钢丝检测档案,结合大数据分析手段,可有效预测钢丝剩余寿命,为石油勘探作业安全提供有力保障。
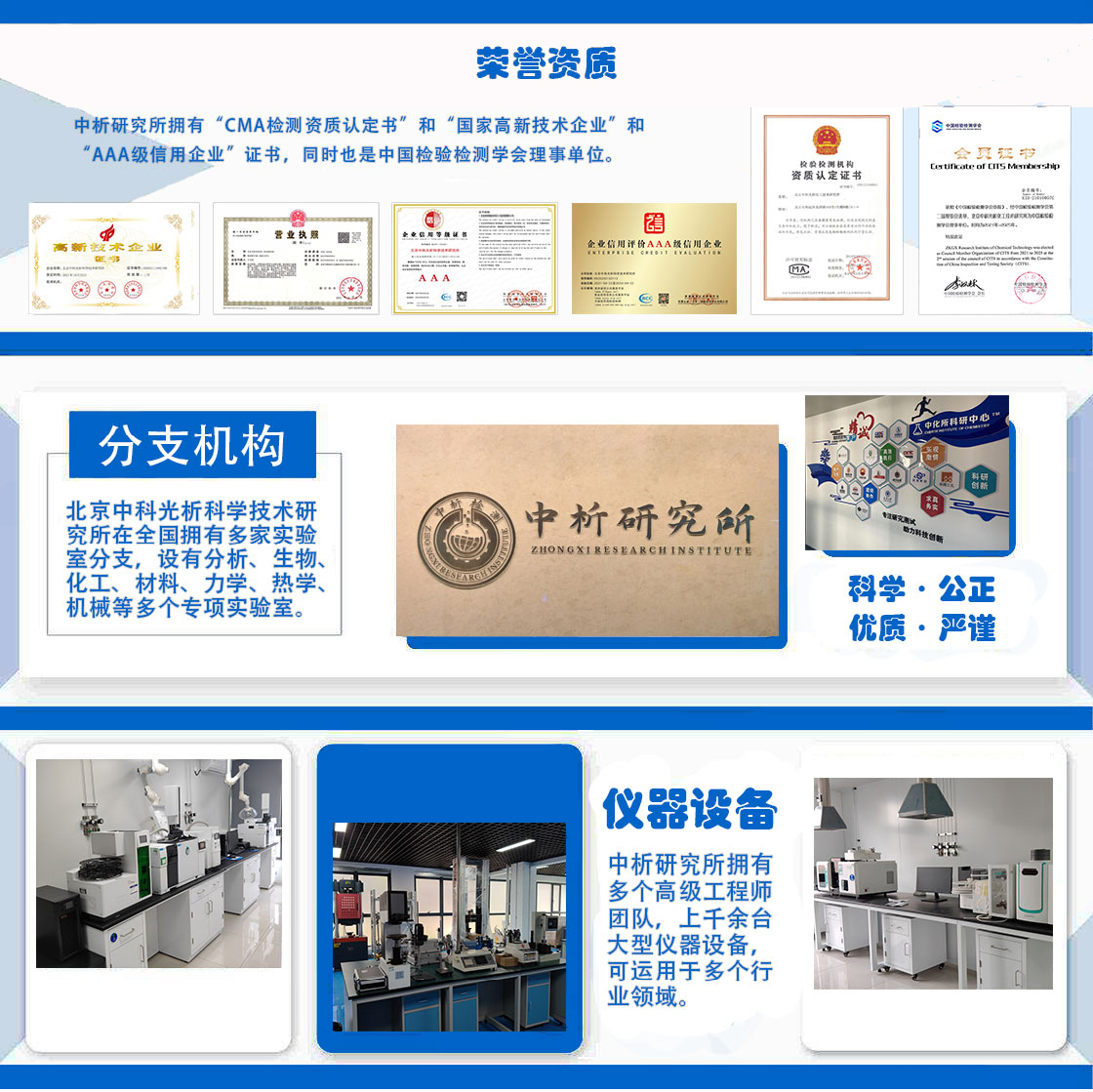
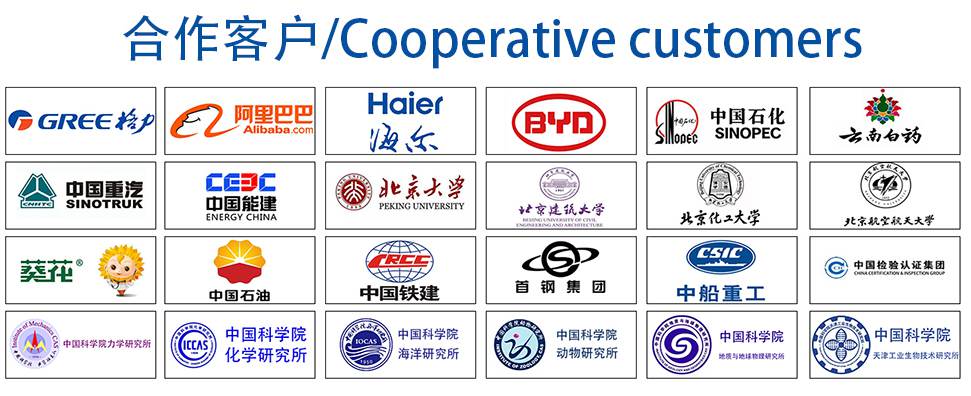