各色汽车用面漆检测的重要性与技术规范
汽车面漆作为车辆最外层的保护与装饰涂层,其性能直接关系到车身的美观性、耐候性和使用寿命。随着消费者对汽车外观品质要求的提升,各色面漆(包括金属漆、珠光漆、素色漆等)的检测成为汽车制造与涂装环节的核心质量控制项目之一。面漆检测不仅需要验证颜色一致性、光泽度等视觉指标,还需通过物理、化学及环境模拟测试评估其抗刮擦性、耐紫外线老化性、耐腐蚀性等综合性能。严格的检测流程可确保不同批次、不同颜色的面漆在不同气候条件下长期保持稳定,避免出现褪色、剥落或开裂等问题。
关键检测项目及方法
1. 颜色与光泽度一致性检测
使用分光测色仪和光泽度计进行量化分析,对比标准色板与实车涂层的L*a*b*色差值(ΔE≤1.0为合格),并验证60°角下的光泽度是否符合设计要求(通常≥90GU)。对于金属漆和珠光漆,还需通过多角度分光仪评估随角异色效应(Flip-Flop Effect)的均匀性。
2. 耐候性测试
模拟极端环境条件,包括:
- QUV加速老化试验:通过紫外线照射(340nm波长)和冷凝循环,评估2000小时后的颜色变化(ΔE≤2.0)和粉化等级(ASTM D4214标准);
- 盐雾试验:依据ISO 9227标准进行1000小时中性盐雾测试,检查漆面起泡、锈蚀情况;
- 高温高湿循环测试:85℃/85%RH环境下进行10个循环(每个循环24小时),观察涂层开裂或附着力下降。
3. 机械性能检测
包括:
- 铅笔硬度测试(ASTM D3363):使用硬度等级≥2H的铅笔验证抗划伤能力;
- 冲击试验(ISO 6272):以1kg重锤从50cm高度坠落,检测漆面抗冲击变形性;
- 附着力测试:通过划格法(ISO 2409)或拉拔法(ASTM D4541)评估涂层与底材的结合强度(0级或≥5MPa为合格)。
4. 耐化学试剂性能
将汽油、制动液、酸雨模拟液(pH4.0)等滴于漆面,24小时后观察是否出现软化、溶胀或变色。高端车型要求通过48小时耐碱性清洁剂(pH10.5)浸泡测试。
5. 特殊功能性检测
针对特殊效果漆面:
- 自修复性能:用划痕修复仪测试微划痕在70℃下的自愈能力;
- 疏水角测量:使用接触角测试仪验证疏水涂层的水滴接触角≥110°;
- 红外反射率:通过分光光度计检测浅色漆的太阳光反射比(TSR≥60%)。
智能检测技术应用趋势
当前主流车企已引入机器视觉系统(如基于AI的色差自动判定)和在线涂层厚度监测仪(ED-XRF/XRF技术),实现生产过程中的实时质量管控。同时,大数据平台可统计分析不同颜色面漆的缺陷分布规律,为工艺优化提供数据支持。
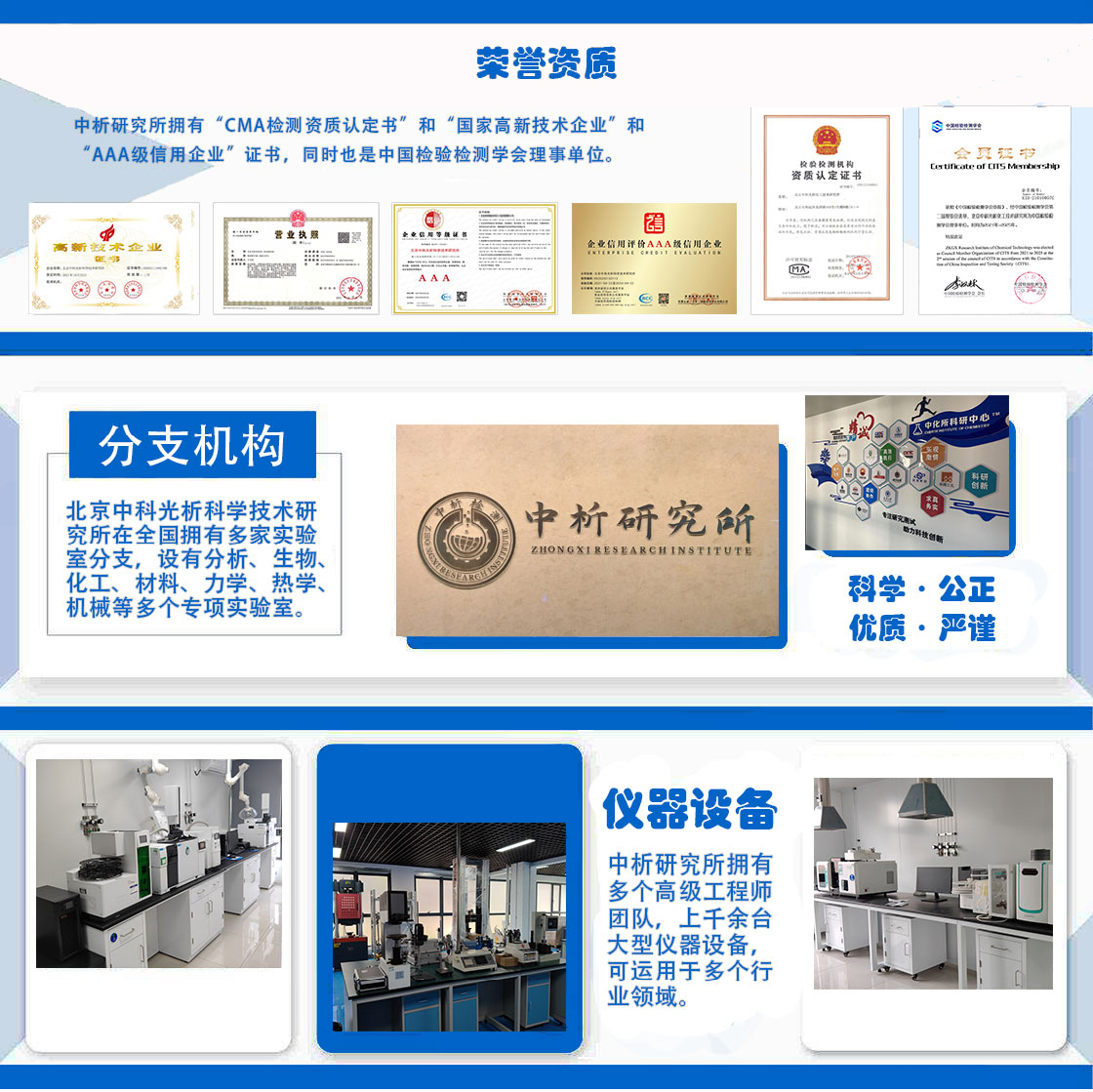
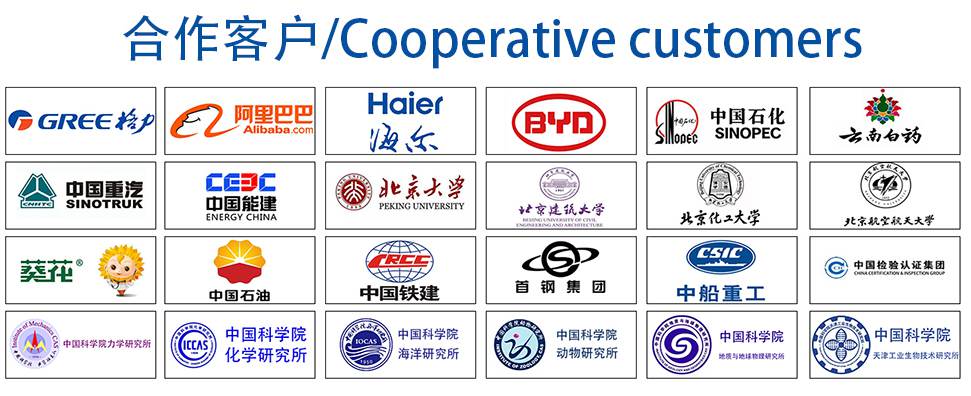