焊钉检测的核心意义与检测项目解析
焊钉作为钢结构、机械设备及建筑幕墙等领域的关键连接件,其焊接质量直接影响工程安全与使用寿命。根据ISO 13918、GB/T 10433等国内外标准要求,焊钉检测需涵盖外观、力学性能、焊接工艺三大维度,并采用目视检查、仪器测量、破坏性试验相结合的检测体系。随着智能制造的发展,2023年新版《钢结构焊接规范》进一步强化了对焊钉焊接缺陷的数字化检测要求,凸显了焊钉质量控制的重要性。
焊钉检测核心项目清单
1. 外观质量检测
使用5倍放大镜进行360°全周目视检查,重点排查焊脚处裂纹、未熔合、咬边等缺陷。通过工业内窥镜对深熔焊钉内部气孔进行观测,要求单个气孔直径不得超过焊钉直径的10%。采用激光轮廓仪对焊缝成形系数(宽高比)进行量化分析,确保符合1.2-1.5的标准范围。
2. 几何尺寸测量
使用数显游标卡尺测量焊后总高度偏差,允许公差±1.5mm。采用焊缝规检测焊脚尺寸,要求角焊缝焊脚K值不低于薄板厚度的0.7倍。对电弧焊钉进行同轴度检测,偏移量不得超过钉杆直径的15%。
3. 力学性能试验
依据ASTM A108标准开展:
• 拉伸试验:采用伺服液压试验机加载至断裂,记录极限抗拉强度(UTS)
• 弯曲试验:使用专用弯曲夹具进行30°冷弯测试,观察表面开裂情况
• 剪切试验:通过双剪试验装置测定剪切强度,要求不低于材料标称强度的70%
4. 无损检测技术应用
针对重要承力部位焊钉实施:
• 超声波检测(UT):采用5MHz探头检测内部未熔合缺陷
• 磁粉检测(MT):对表面及近表面裂纹进行荧光磁粉探查
• 射线检测(RT):通过数字成像系统(DR)分析根部熔透情况
5. 金相组织分析
制取焊接接头横截面试样,经研磨抛光后使用金相显微镜观察:
• 熔合区宽度控制在0.1-0.5mm
• 热影响区(HAZ)硬度不超过母材的120%
• 马氏体含量<10%(低合金钢焊钉)
智能化检测新趋势
当前行业正推广基于机器视觉的自动检测系统,采用2000万像素工业相机配合深度学习算法,可实现焊钉缺陷的实时分类识别。同时,焊接过程监控系统可记录电流电压波形、电弧能量分布等40余项工艺参数,利用大数据分析预测焊接质量,推动焊钉检测进入智能化时代。
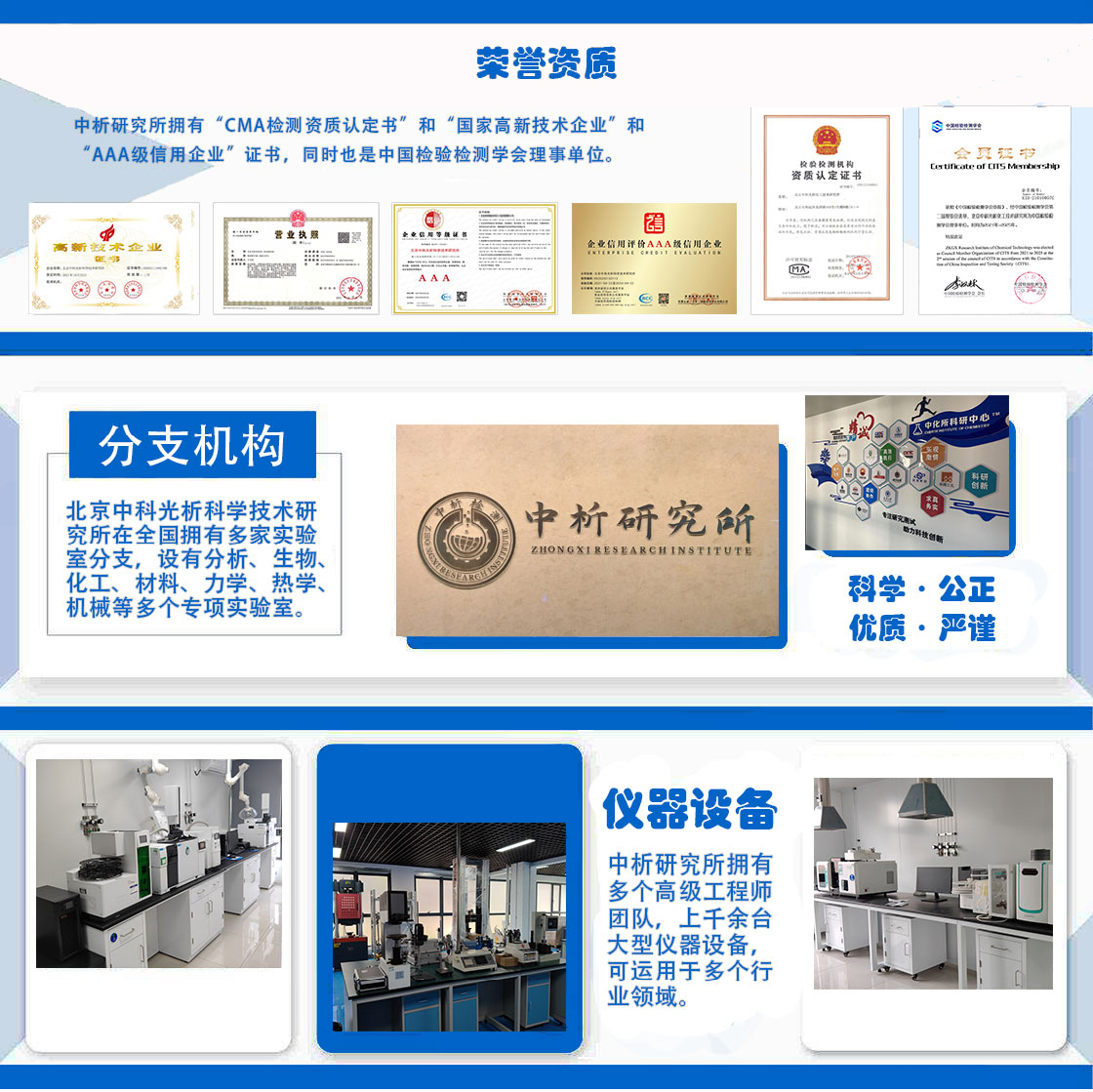
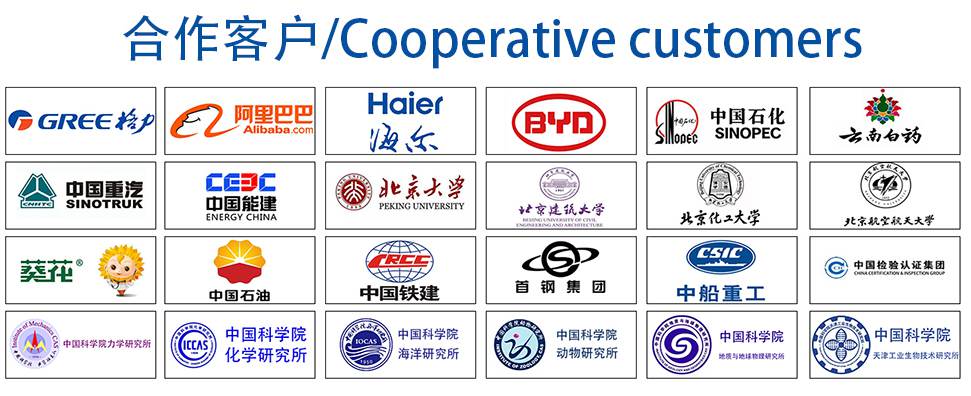