球节点检测的技术要点与应用场景
球节点检测是机械制造、建筑工程及特种设备维护领域的关键技术,主要针对球形连接结构的完整性、力学性能和使用安全性进行系统性评估。球节点作为传递载荷、调节运动方向的重要组件,广泛应用于桥梁钢结构、工程机械臂、汽车转向系统以及航天器关节结构中。其检测需求源于长期承受动态应力、环境腐蚀或材料老化可能引发的安全隐患。传统检测通常采用目视检查结合物理测量,而现代技术则融合三维扫描、超声波探伤和材料光谱分析,形成多维度检测体系,以确保球节点的几何精度、表面质量和内部结构满足行业标准。
核心检测项目与实施方法
1. 几何尺寸精度检测
使用三坐标测量仪(CMM)或激光扫描仪对球体直径、圆度误差进行微米级测量,重点监测球面与连接杆的同心度偏差。对于直径超过500mm的大型球节点,需采用分段扫描与数据拼接技术,确保测量覆盖率达到95%以上。
2. 表面缺陷检测
通过磁粉探伤(MT)识别表面裂纹,渗透检测(PT)发现微米级气孔,配合20倍工业内窥镜观察内部接触面磨损状况。对海上平台用球节点还需进行盐雾腐蚀深度测定,使用显微硬度计评估表层材料退化程度。
3. 材料性能检测
采用光谱分析仪进行合金成分验证,确保材料符合ASTM A668或EN 10025标准。通过金相显微镜观察晶粒结构,配合拉伸试验机测试屈服强度(通常要求≥355MPa),对核电等特殊场景还需进行-40℃低温冲击试验。
4. 动态承载测试
搭建液压伺服加载系统模拟实际工况,连续施加交变载荷至设计极限的1.5倍,监测节点是否发生塑性变形。同步采集振动频谱数据,通过有限元分析验证理论模型与实际性能的吻合度,疲劳寿命测试周期通常不少于5×10^6次循环。
5. 密封性能检测
对带有润滑通道的封闭式球节点,采用氦质谱检漏法检测密封性,泄漏率需控制在1×10^-6 mbar·L/s以下。高压注水试验时,维持30MPa压力持续2小时,观察表面是否出现渗漏痕迹。
智能化检测技术发展
随着工业4.0技术的普及,基于机器视觉的自动化检测系统已能实现0.02mm的缺陷识别精度。无人机搭载热成像仪可完成高空球节点的快速巡检,而数字孪生技术通过建立三维力学模型,可预测节点在不同工况下的应力分布状态。这些技术的融合显著提升了检测效率,使球节点故障预警准确率提升至98%以上。
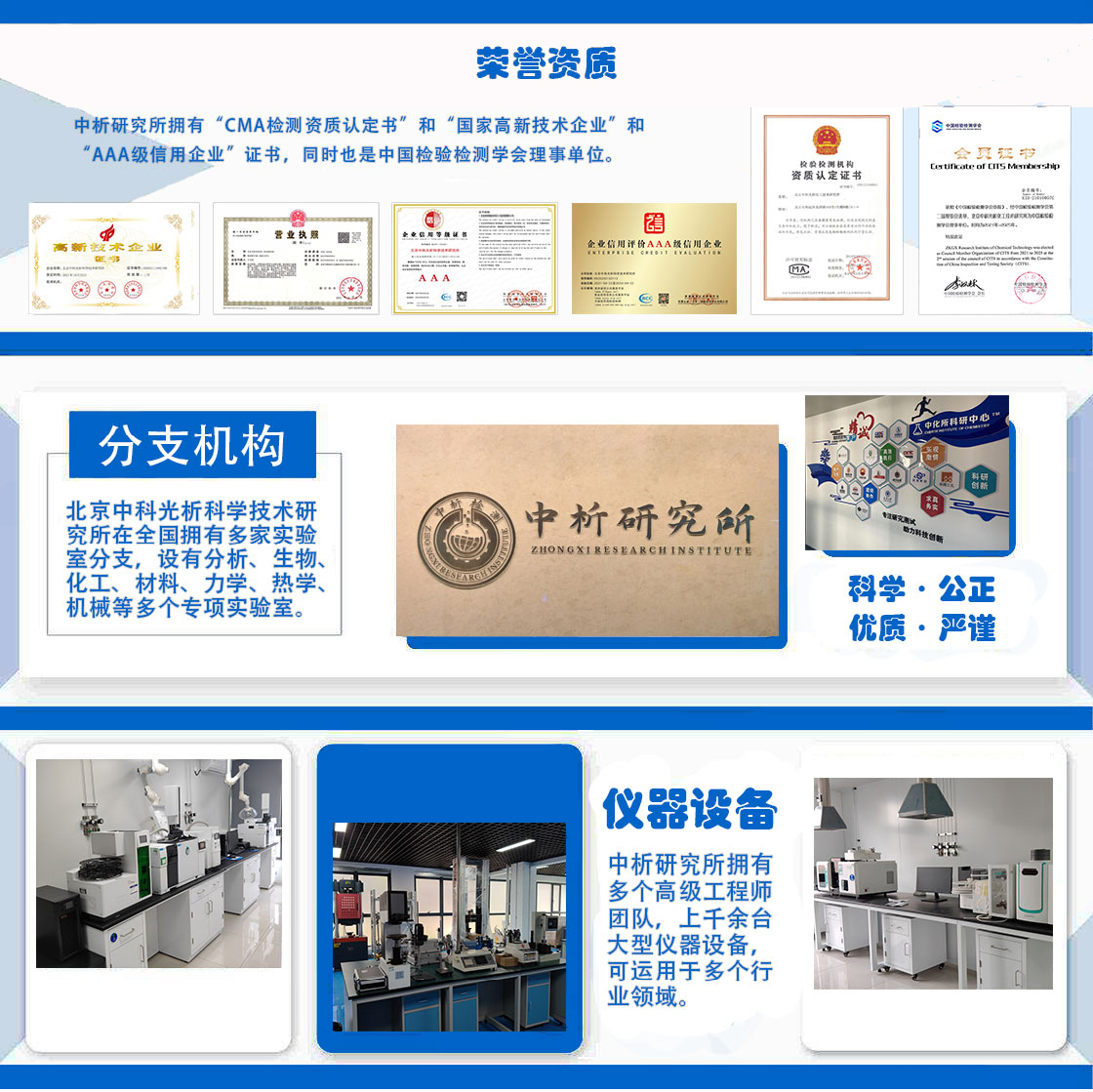
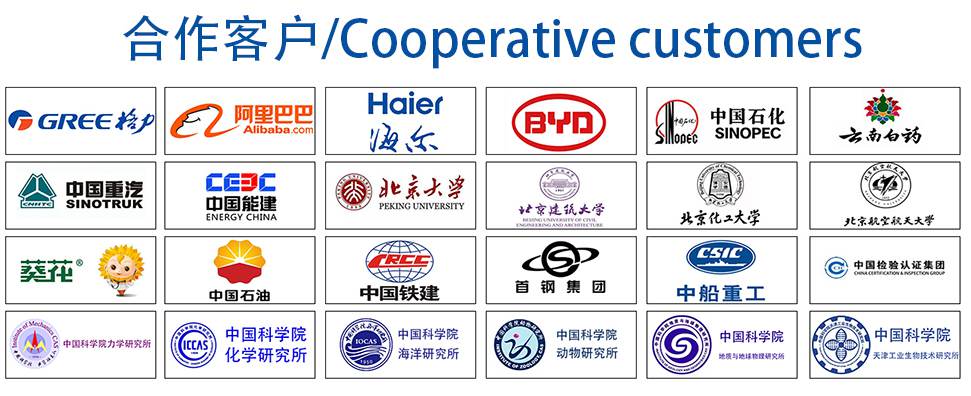