电动汽车用动力蓄电池检测:保障安全与性能的核心环节
随着电动汽车产业的快速发展,动力蓄电池作为车辆的"心脏",其安全性、可靠性和耐久性直接关系到整车的性能表现与用户使用体验。为应对高温、过充、碰撞等极端工况带来的风险,动力蓄电池需经过严格的全生命周期检测验证,涵盖电化学性能、机械安全、环境适应性等多个维度。行业监管部门与车企共同构建了覆盖电池研发、生产到应用的检测体系,以确保产品符合国家标准(如GB 38031-2020)和国际规范(如UN GTR 20)。
一、电化学性能检测
通过充放电循环测试仪评估电池的容量保持率、能量效率等核心指标,验证电池在深度放电(DOD 80%)条件下的循环寿命。采用电化学阻抗谱(EIS)分析电池内阻变化,建立SOC(荷电状态)与SOH(健康状态)的精准对应模型。例如,按GB/T 31486要求,电池组在-20℃低温环境下仍需保持标称容量的70%以上。
二、机械安全测试
依据GB 38031标准进行多维度物理安全验证:包括200kN挤压力下的壳体变形测试、模拟碰撞的加速度冲击试验(50g/15ms)。特别针对热失控防护,要求电池包在针刺触发单体热失控后,系统能在5分钟内不起火不爆炸。最新标准新增了底部球击试验,模拟车辆托底时电池包的抗冲击能力。
三、环境适应性验证
在温湿度交变箱中模拟-40℃至85℃的极端气候,连续进行72小时高低温循环测试。湿热试验要求电池在40℃/95%RH环境中保持500小时性能稳定。振动测试需满足随机振动谱(20Hz-2000Hz)和定频振动(28Hz/30g)双重标准,模拟10万公里道路载荷对电池结构的考验。
四、热管理系统检测
通过红外热成像仪监测电池组温度场分布,验证液冷系统在3C快充时的温控能力。热扩散测试要求模组内任意单体触发热失控后,系统能在60分钟内阻止火势蔓延。最新检测规程新增了热失控气体成分分析,对CO、HF等有毒气体的释放量设定了严格限值。
五、BMS功能验证
电池管理系统(BMS)需通过HIL台架测试,验证过压/欠压保护、绝缘监测等28项核心功能。SOC估算精度要求在全程工况下误差≤5%,均衡功能测试需达到单体电压差<20mV。针对电磁兼容性,需通过ISO 11452-2标准的辐射抗扰度测试(200V/m场强)。
随着固态电池、钠离子电池等新技术的产业化推进,检测体系正在向多维评价方向发展。第三方检测机构通过搭建"材料-单体-模组-系统"四级测试平台,结合大数据寿命预测模型,为动力蓄电池的全生命周期管理提供技术支撑。只有通过严苛的检测验证,才能确保动力蓄电池在能量密度与安全性之间取得最佳平衡,推动电动汽车产业可持续发展。
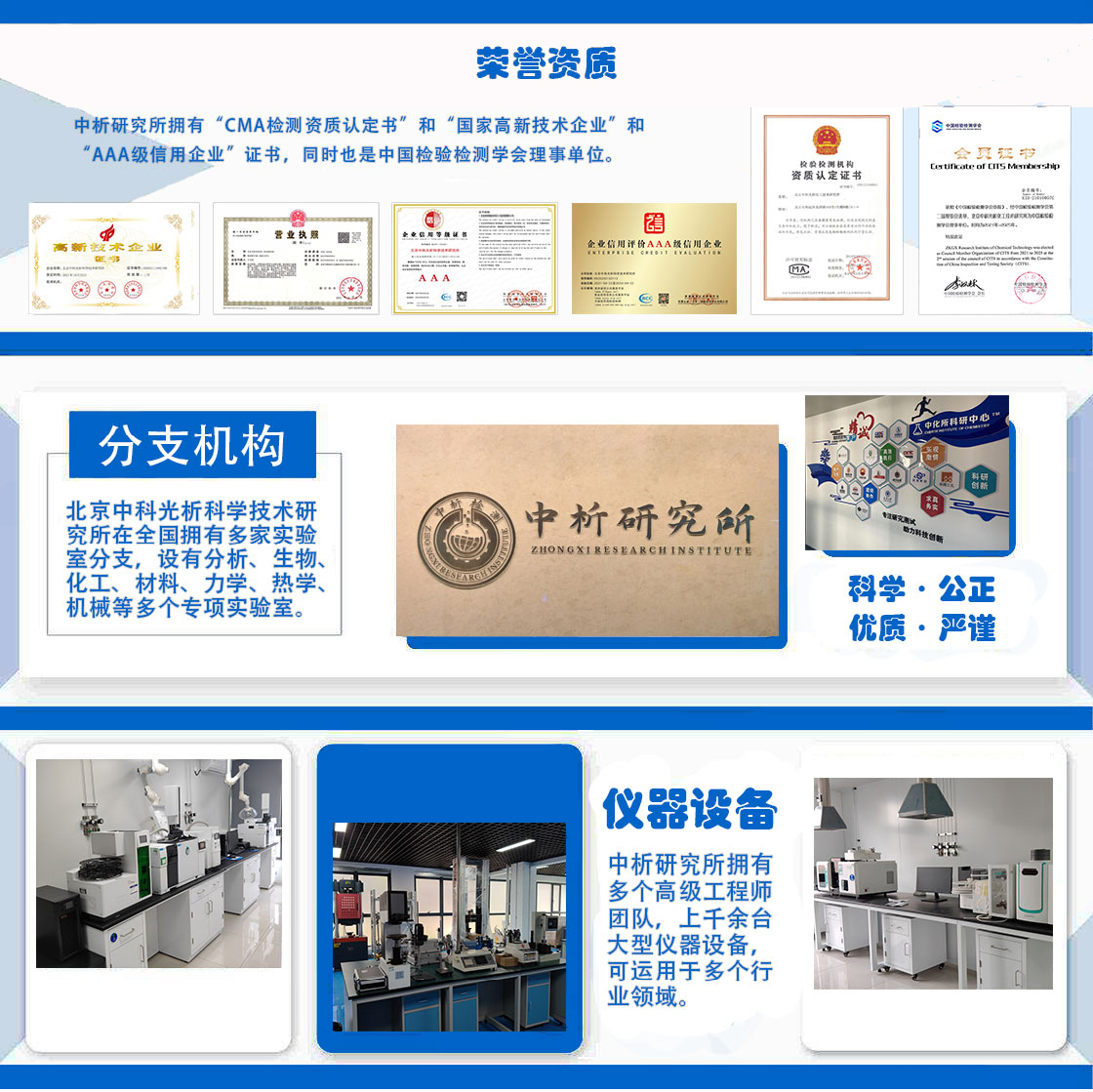
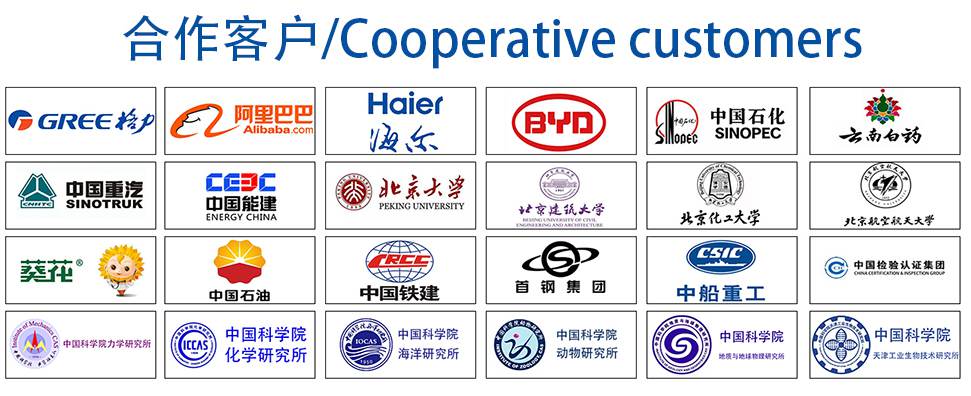