鞋和箱包用胶粘剂检测的重要性
在鞋类、箱包等皮革制品的生产过程中,胶粘剂是决定产品质量和使用寿命的核心材料。随着消费者对产品安全性和环保性的关注度提升,胶粘剂的物理性能、化学稳定性及有害物质含量已成为行业监管的重点。专业检测不仅能验证粘合强度是否符合使用需求,更能排查潜在的有害物质超标风险,避免因粘接失效或化学污染导致的产品召回问题。目前国内外针对胶粘剂的检测已形成包含20余项指标的完整体系,覆盖从基础物理性能到环保安全的多个维度。
核心检测项目及标准
一、物理性能测试
1. 拉伸剪切强度(GB/T 7124):通过万能材料试验机测定胶层在拉伸状态下的最大破坏载荷,箱包类产品要求≥5MPa,运动鞋底胶需达到≥8MPa
2. 剥离强度(GB/T 2791):模拟产品开胶场景,使用90°剥离法测试,皮鞋帮底结合处要求≥60N/cm
3. 耐温性测试:-20℃至80℃环境下循环处理后的强度保留率需>85%
4. 耐水性测试:浸水72小时后粘结强度衰减不超过30%
二、化学成分分析
1. VOC含量检测(HJ 2541):通过气相色谱法测定苯、甲苯、二甲苯等挥发物,鞋用胶要求总VOC<350g/L
2. 甲醛释放量(GB 18583):酚醛树脂类胶粘剂需控制游离甲醛≤1.0g/kg
3. 重金属检测(EN 71-3):针对铅、镉、汞等8项指标,儿童箱包材料需满足迁移量<10ppm
4. 邻苯二甲酸酯(REACH法规):DBP、BBP、DEHP等增塑剂总含量<0.1%
三、特殊功能测试
1. 抗老化性能:氙灯老化箱模拟200小时光照后粘结强度保留率>80%
2. 耐油脂测试:接触人工汗液或油脂介质后的粘接性能变化率<15%
3. 低温脆性:-30℃环境下进行180°弯折测试不应出现胶层开裂
4. 固化速度:通过热重分析法测定不同温度下的表干时间和完全固化时间
检测流程优化建议
生产企业应建立从原料验收到成品抽检的三级质量控制体系:
1. 原材料入库前进行批次抽样全项检测
2. 生产过程中每2小时监控胶水粘度、固含量等工艺参数
3. 成品批次按ISO 2859-1标准进行AQL抽样检验
4. 每年委托第三方实验室进行RoHS、REACH等法规符合性验证
常见质量问题解析
1. 开胶问题:通常由固化不完全或基材表面处理不当引起,可通过红外光谱分析胶层交联度
2. 黄变现象:紫外线吸收剂添加不足导致,需检测耐候性指标
3. 刺鼻气味:甲苯等溶剂残留超标,应优化干燥工艺参数
4. 胶膜脆裂:增塑剂配比失衡,需复核DIN EN 1465标准的柔韧性测试数据
结语
完善的胶粘剂检测体系是保障鞋箱包产品品质的关键防线。随着GB 33372-2020《胶粘剂挥发性有机化合物限量》等新标准的实施,企业需及时更新检测方案,特别关注生物基胶粘剂等新型材料的特殊检测需求。通过科学的检测数据指导配方优化,才能在提升产品性能的同时满足日趋严格的环保法规要求。
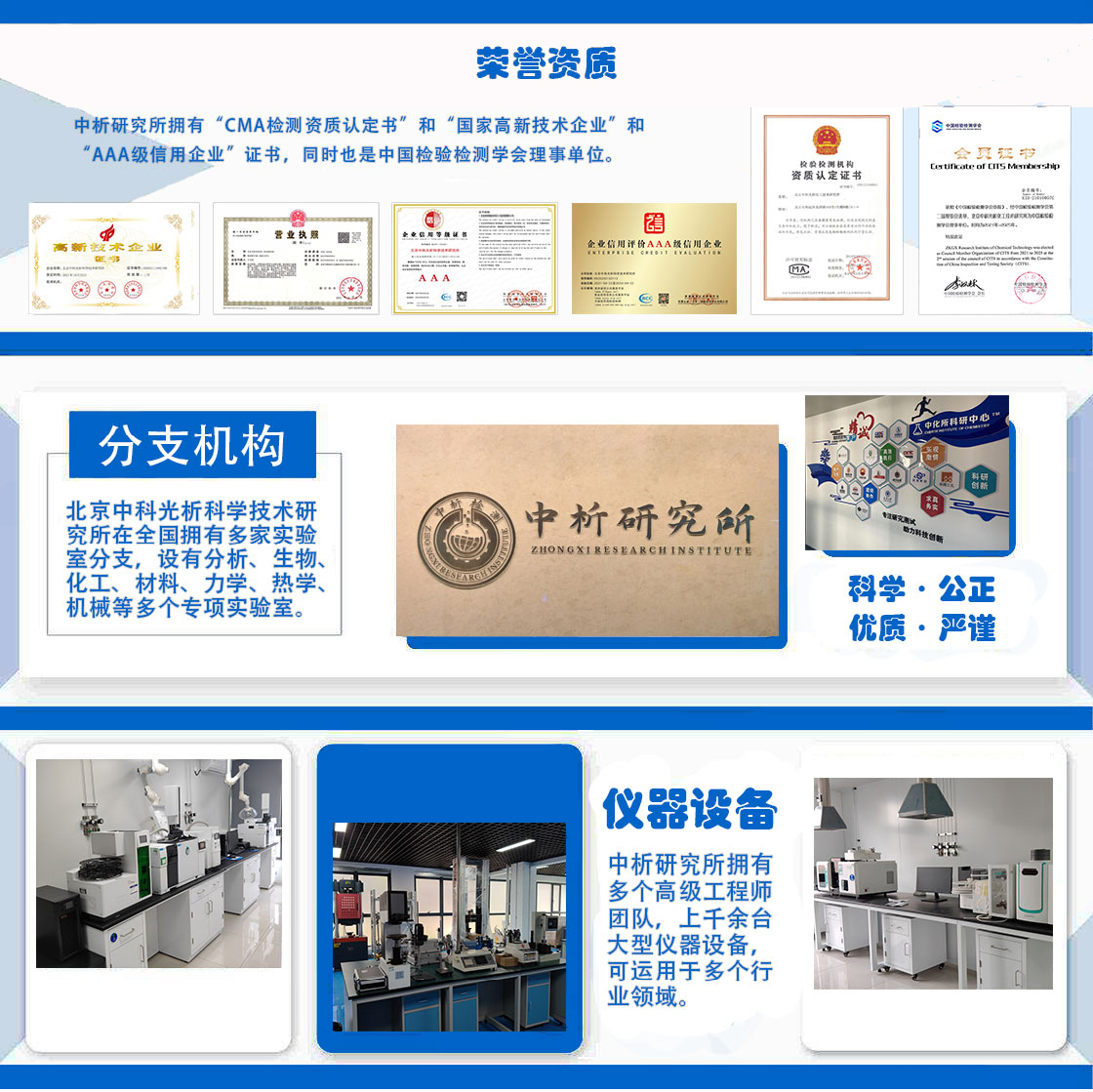
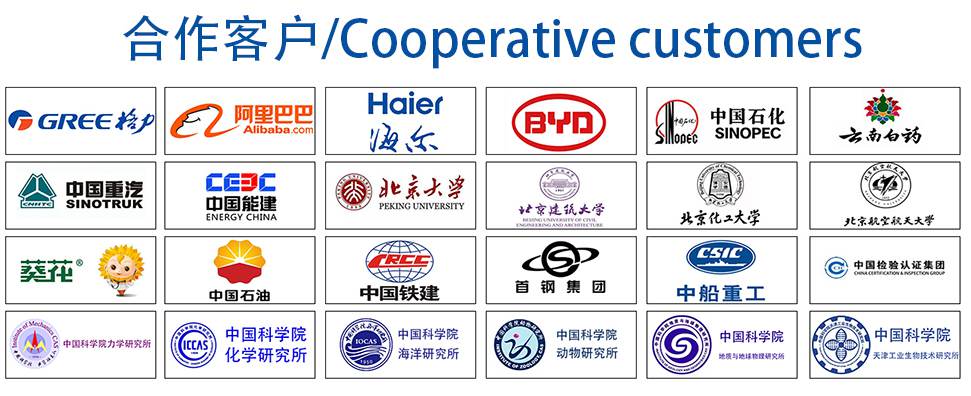