汽车用制动器衬片检测的重要性
作为汽车制动系统的核心安全部件,制动器衬片的性能直接关系到行车安全与驾驶体验。根据国家强制标准GB 5763-2018《汽车用制动器衬片》规定,所有上市销售的刹车片必须通过20余项严格检测,涉及摩擦性能、耐久性、环保指标等关键参数。随着汽车工业向新能源、轻量化方向发展,对刹车片的热稳定性、抗衰减能力和NVH(噪音振动)表现提出了更高要求,这使得检测工作不仅要符合现行标准,更要适应技术迭代带来的新型检测需求。
核心检测项目解析
1. 摩擦性能测试
采用定速式摩擦试验机,在100-350℃温度范围内模拟不同工况,检测摩擦系数(μ)随温度变化的稳定性。依据QC/T 237-2021标准,要求摩擦系数波动范围≤±15%,特别在高温段(300℃以上)不得出现明显衰减。最新检测方法增加了制动压力脉动模拟,更真实反映紧急制动时的动态摩擦特性。
2. 磨损率测定
通过台架试验累计500次制动循环,使用激光轮廓仪测量衬片厚度变化。行业标准要求乘用车刹车片平均磨损率≤0.15mm/万公里,商用车重型刹车片需≤0.25mm/万公里。值得注意的是,新型陶瓷配方材料的磨损率检测需特别关注冷态磨损特性,这与传统半金属材料存在显著差异。
3. 热稳定性验证
在650℃高温炉中进行连续24小时老化试验,检测材料膨胀率、硬度变化及表面裂纹情况。优质产品热膨胀系数应≤3×10⁻⁶/℃,硬度变化率≤15%。针对电动汽车能量回收系统导致的低频次高负荷制动特点,新增了间歇性高温冲击试验(650℃→常温循环100次)。
4. 剪切强度检测
使用万能材料试验机进行背板与摩擦材料的剥离测试,根据GB/T 22309标准,剪切强度需≥6.5MPa。新能源汽车因整备质量增加,部分车型要求提升至8.0MPa以上。检测过程中需特别注意界面粘接层的微观结构分析,防止出现气孔、夹杂等隐性缺陷。
5. 环保性能评估
依据欧盟REACH法规和GB/T 30512-2014标准,重点检测铜含量(需<0.5%)、石棉残留(必须未检出)及挥发性有机物(VOCs)。最新检测体系新增了制动粉尘PM2.5排放测试,要求每公里制动产生的可吸入颗粒物≤5mg,这对摩擦材料的配方设计提出了革命性要求。
检测技术发展趋势
随着智能化检测设备的普及,基于机器视觉的表面缺陷自动识别系统已实现97%以上的检测准确率。虚拟现实(VR)技术被应用于台架试验工况模拟,可精确还原冰雪路面、连续弯道等复杂场景。2023年实施的《智能网联汽车制动系统检测规范》更要求刹车片配备芯片级传感器,实现磨耗状态的实时监测与预警。
专业的检测机构不仅需要配备价值千万的惯性试验台、噪声振动分析系统等硬件设备,更要建立覆盖原材料采购、生产工艺、成品检测的全链条质量追溯体系。消费者在选择刹车片时,应重点关注检测报告中的摩擦系数曲线、高温衰减率、环保认证等核心指标,确保产品既符合国标要求,又能满足特定车型的个性化制动需求。
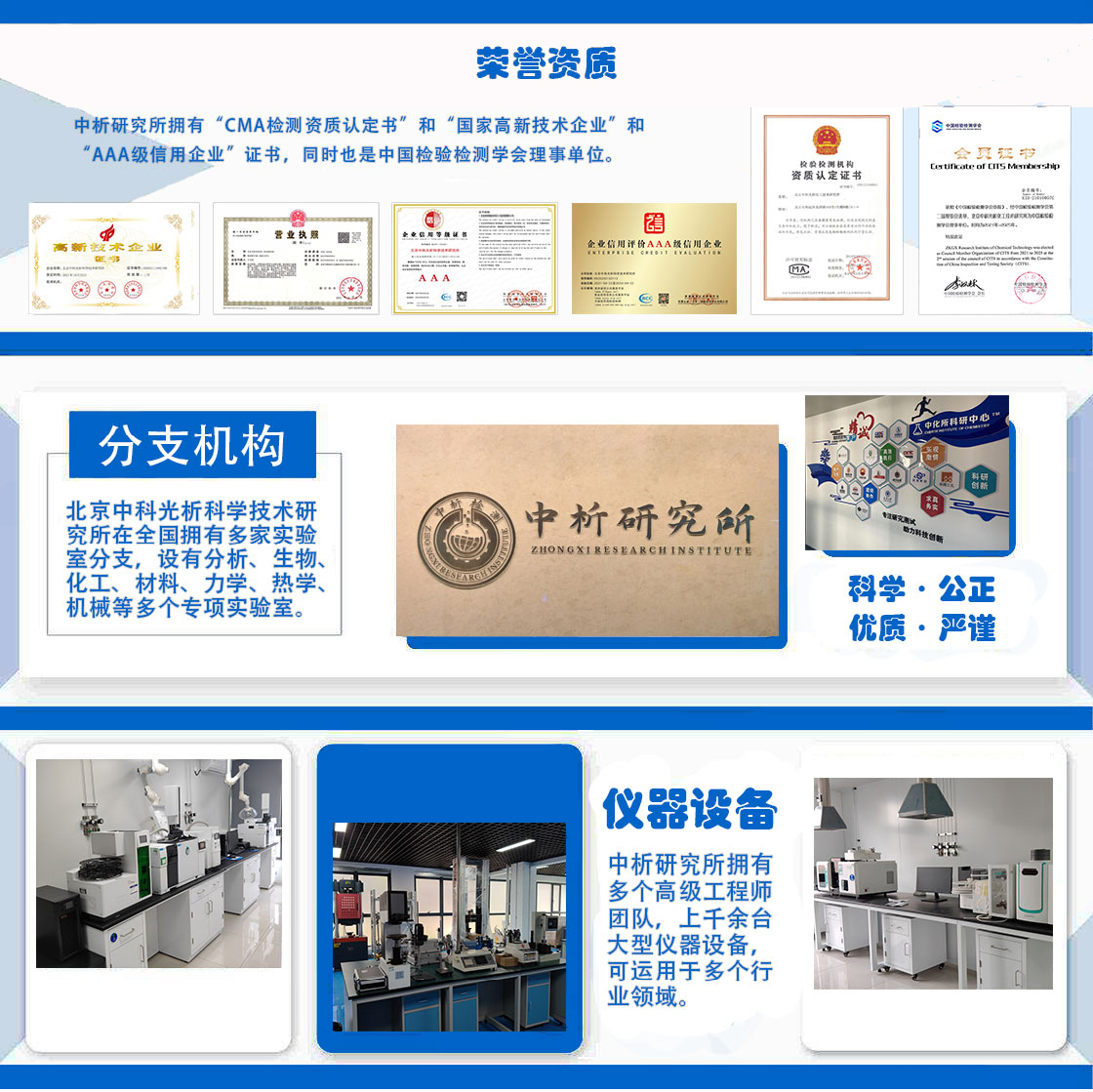
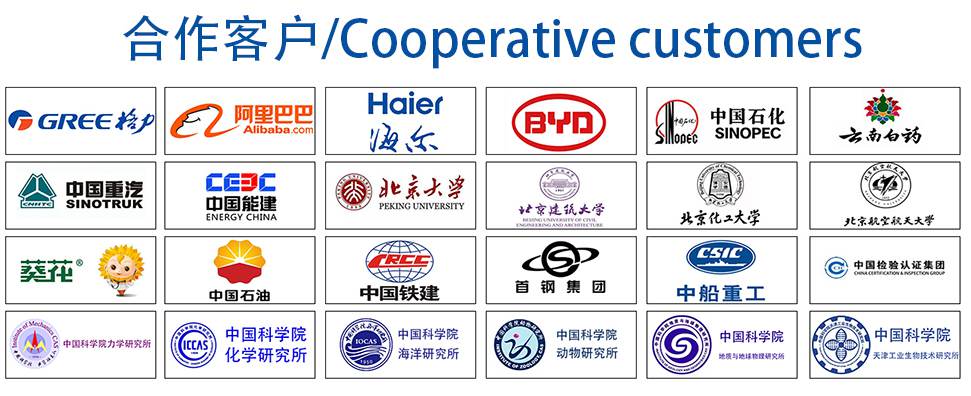