汽车内外饰零部件及材料靠背骨架总成耐久性试验检测
实验室拥有众多大型仪器及各类分析检测设备,研究所长期与各大企业、高校和科研院所保持合作伙伴关系,始终以科学研究为首任,以客户为中心,不断提高自身综合检测能力和水平,致力于成为全国科学材料研发领域服务平台。
立即咨询汽车内外饰零部件及材料靠背骨架总成耐久性试验检测
汽车内外饰零部件及材料靠背骨架总成耐久性试验检测
在现代汽车制造业中,内外饰零部件及材料不仅影响整车的美观和舒适性,更直接关系到车辆的安全性和使用寿命。其中靠背骨架作为座椅结构的重要组成部分,其耐久性测试尤为关键。耐久性试验检测旨在评估零部件在长期使用中的性能稳定性,以确保其能够承受驾驶条件下的多种压力与疲劳负荷。
靠背骨架的结构与功能
靠背骨架通常由金属和高强度复合材料构成,它是座椅的重要支撑结构,必须满足人体工程学设计要求,同时为车辆在碰撞时提供安全保护。其结构设计要求在轻量化的前提下,具备充足的强度和韧性,以承担车辆在急加速、急刹车及高速过弯时产生的动态载荷。
现代汽车设计中,靠背骨架与内饰材料的结合愈发紧密,在舒适性与安全性之间找到最佳平衡是厂商们不断追求的目标。因此,针对靠背骨架的耐久性测试不仅要考量材料的物理属性,还要考虑结构设计的合理性和装配工艺的影响。
耐久性试验检测的必要性
耐久性试验能够模拟车辆在实际行驶环境下的长时间使用,对零部件所可能遭遇的各类应力进行预测和测试。这些应力来源不仅包括车辆行驶过程中的振动和冲击,还有温度变动、湿度变化以及化学介质的侵蚀。这些因素都可能导致材料的疲劳失效、结构变形甚至断裂。
对靠背骨架进行耐久性试验可以提前发现设计缺陷或材料瑕疵,从而在产品批量生产之前进行优化设计,避免一旦投放市场造成大规模召回和使用安全隐患。此外,检测结果也能为厂商提供产品升级改进的科学依据,在竞品中脱颖而出。
试验方法与流程
靠背骨架总成的耐久性试验通常包括静态加载试验、动态疲劳测试以及环境模拟试验等步骤。每一项测试均按照特定的标准和规范进行,以确保结果的准确性和可比性。
1. 静态加载试验:
该测试主要通过施加逐步增加的力来评估靠背骨架的极限承载能力。测试时会按照预定的加载路径施加压力,直到骨架发生明显变形或破坏,以评估材料的强度和韧性。
2. 动态疲劳测试:
动态疲劳测试重点在于验证靠背骨架在重复受力条件下的耐疲劳性能。通过模拟座椅在车辆运行过程中的真实振动环境进行循环加载试验,以此检测零部件在高频应力交变下的使用寿命和损伤演变过程。
3. 环境模拟试验:
这部分试验主要模拟靠背骨架在不同环境因子作用下的耐久性能。例如,温度试验会在较宽的温度范围内进行测试以检验材料的膨胀系数和热疲劳特性;同时,盐雾试验、湿度试验会检测材料抗腐蚀性及在极端条件下的稳定性。
检测结果的分析与应用
试验结束后,要对各种测试数据进行系统分析,以判断靠背骨架的可靠性和安全性。分析内容包括但不限于材料的应力应变关系、裂纹扩展情况以及座椅整体结构的变形量等指标。基于此类分析,工程师能够识别材料的弱点或设计上的缺陷,并制定改进方案。
检测结果不仅体现在实验室数据上,还需与实际道路测试结果结合,为汽车设计提供全面的技术支持。在这些数据的基础上,制造商可以进行材料的迭代开发、生产工艺的调整以及整车设计的优化,从而提升产品的市场竞争力。
与展望
通过耐久性试验检测,能够全方位评估汽车内外饰零部件及材料的性能,为消费者提供安全舒适的驾驶体验,同时也为厂商在产品研发阶段提供关键技术支持。在绿色环保和智能化趋势的推动下,未来的汽车设计将更加注重材料的节能环保和智能反馈能力。因此,耐久性检测也需要不断创新和发展,以适应新材料新技术的应用。
未来,随着汽车工业技术的不断进步,耐久性测试手段将更加多样化和精准化。自动化测试设备和人工智能技术的引入,将使测试效率和准确性得到显著提高。在此背景下,靠背骨架的耐久性测试也将为汽车制造业的高质量发展贡献更多的力量。
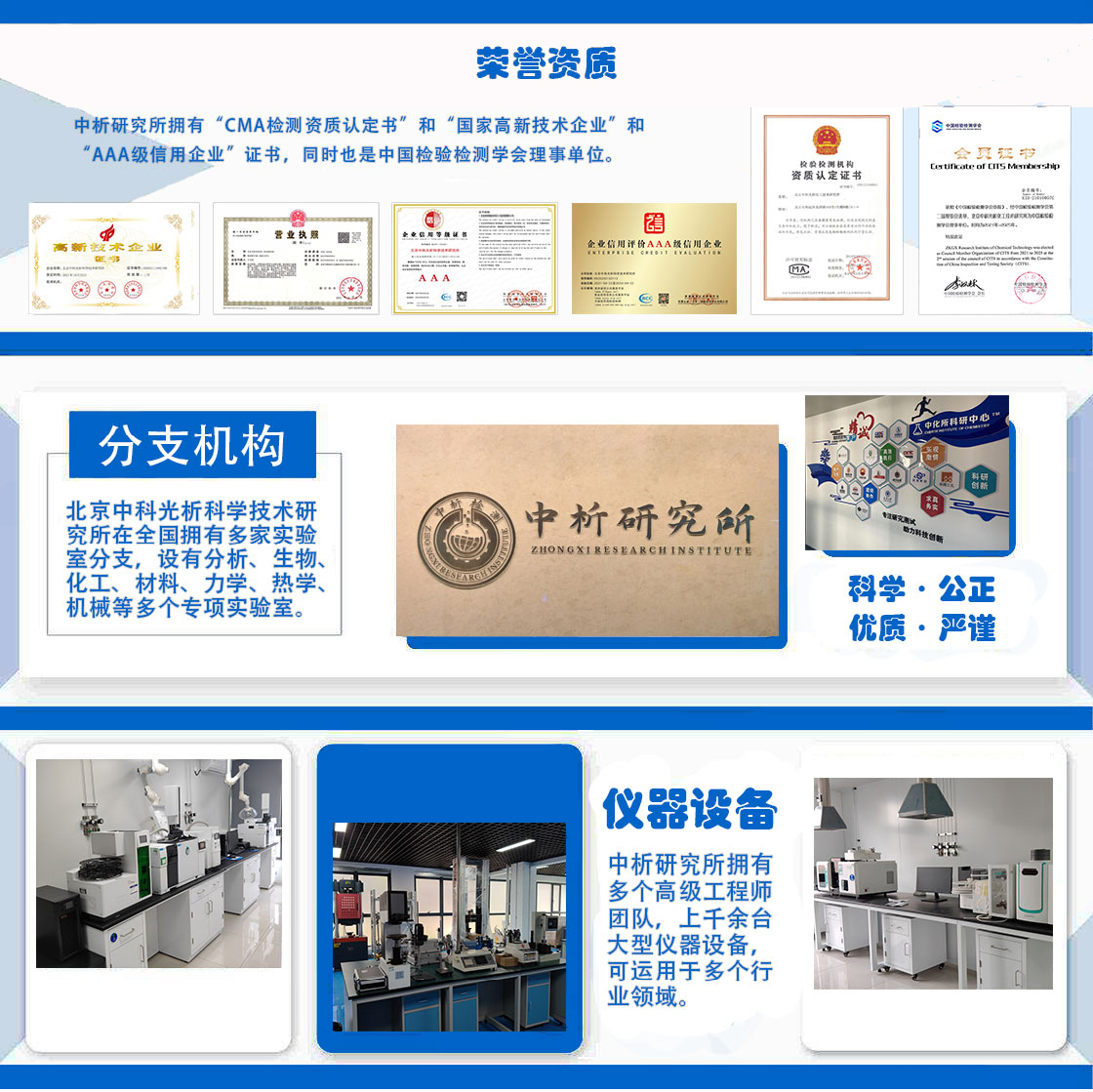
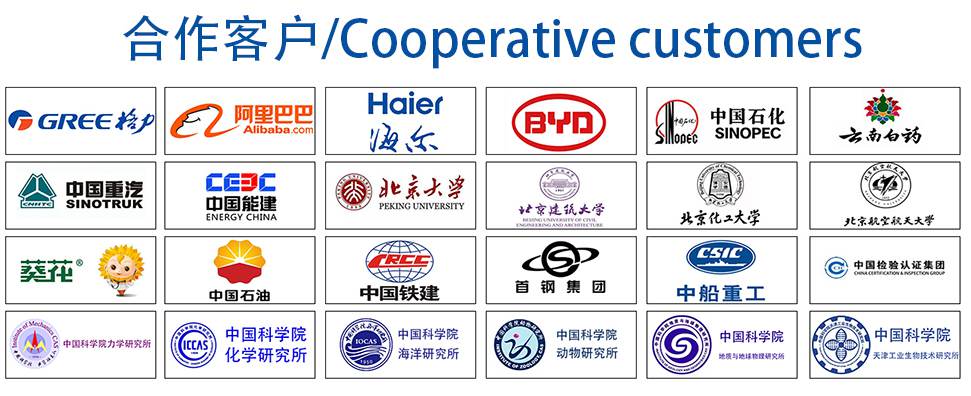