气制动用储气筒检测
实验室拥有众多大型仪器及各类分析检测设备,研究所长期与各大企业、高校和科研院所保持合作伙伴关系,始终以科学研究为首任,以客户为中心,不断提高自身综合检测能力和水平,致力于成为全国科学材料研发领域服务平台。
立即咨询气制动用储气筒检测项目及技术要点解析
气制动用储气筒作为商用车、工程机械等车辆气制动系统的核心部件,承担着储存压缩空气、稳定系统压力、保障制动可靠性的关键作用。其性能直接关系到行车安全与制动响应效率。为确保储气筒长期稳定运行,需通过系统性检测评估其结构完整性、密封性能和承压能力。以下是气制动用储气筒检测的核心项目及技术要求。
一、结构完整性检测
1. 外观检查:通过目视或工业内窥镜观察储气筒内外表面,排查凹陷、裂纹、焊接缺陷等机械损伤,重点关注筒体与端盖连接部位。2. 壁厚测量:利用超声波测厚仪多点检测筒体壁厚,确保符合GB/T 19905-2017规定的壁厚公差(通常不低于设计值的90%)。
二、气密性检测
采用气压试验法,向储气筒注入1.5倍额定工作压力(常规车辆为0.8-1.0MPa)的干燥空气,保压3分钟后用肥皂水涂抹检测所有焊缝、接口及阀门连接处,要求泄漏量不超过0.1kPa/min。智能检测系统可同步监控压力衰减曲线实现精准判定。
三、安全阀与压力表功能验证
1. 安全阀开启压力测试:在专用试验台上逐步加压至安全阀起跳,实测值应处于额定压力(1.2-1.3倍工作压力)的±5%范围内。2. 压力表精度校准:对比储气筒压力表与标准压力传感器读数,示值误差需满足JJG 52-2013规程要求的±2.5%精度等级。
四、容积参数检测
通过注水法或三维激光扫描测量有效容积,实测值需与标称容积偏差≤3%。特殊车型需按照QC/T 200-2022标准进行容量-压力响应特性测试,验证供气效率是否满足连续制动需求。
五、材料性能检测
1. 耐压试验:模拟极限工况进行爆破试验,爆破压力应≥3倍工作压力。2. 盐雾腐蚀试验:按GB/T 10125标准进行720小时中性盐雾测试,表面锈蚀面积不得超过5%。3. 材料金相分析:对取样材料进行显微组织检测,确保无夹渣、气泡等冶金缺陷。
六、安装稳固性检查
使用扭力扳手复紧固定支架螺栓,扭矩值应符合车辆制造商技术规范(通常为80-120N·m)。振动台模拟试验中,储气筒在10-500Hz随机振动条件下不得出现结构性共振,支架位移量应<0.5mm。
通过上述检测项目可全面评估储气筒的可靠性,建议每2年或行驶10万公里进行定期检测,同时结合智能传感器实现压力、温度等参数的实时监控,构建主动预防性维护体系。检测过程中应严格遵循TSG 21-2016《固定式压力容器安全技术监察规程》及相关行业标准,确保检测数据的法律效力与可比性。
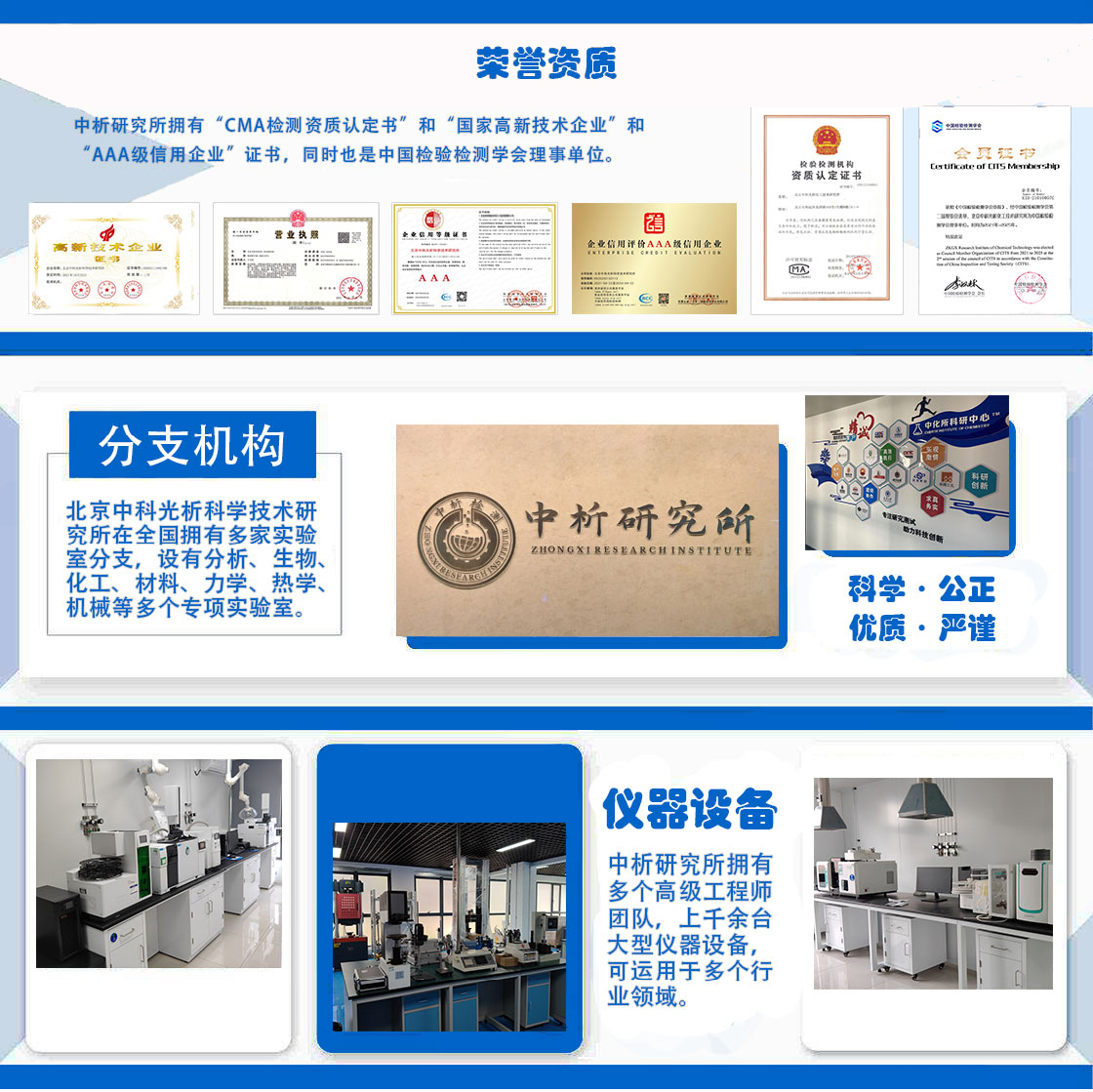
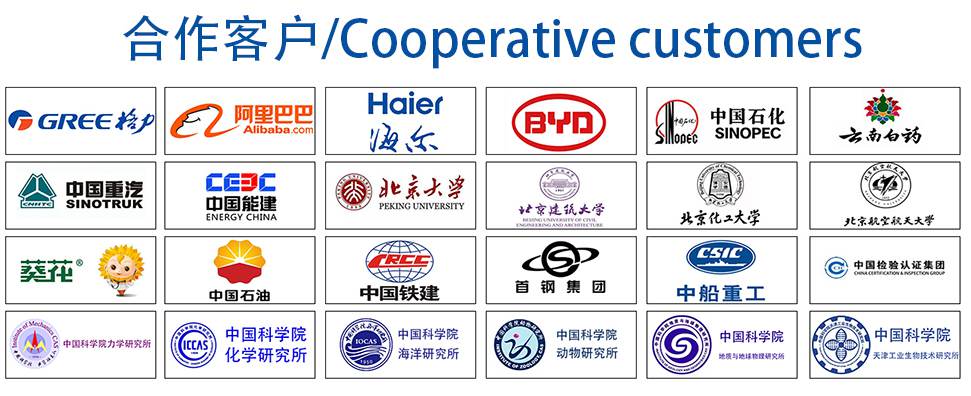